Navigating the Evolving Landscape: Key Trends, Technologies, and Challenges Shaping the Dental Lab Industry in 2025
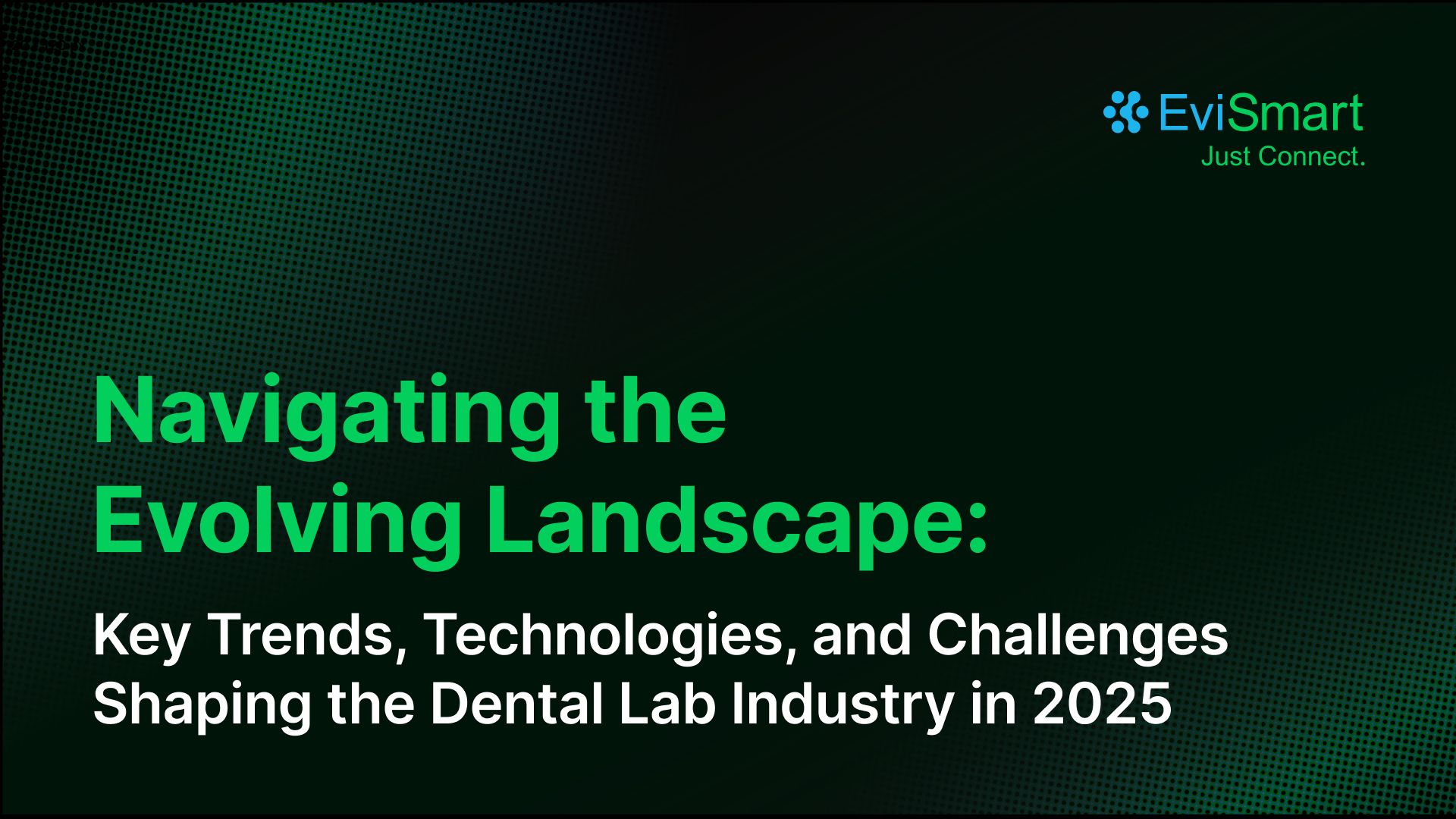
1. Introduction: The Dental Lab Industry at a Crossroads
The dental laboratory industry, a vital yet often under-recognized segment of the broader dental care ecosystem, stands at a significant inflection point. Tasked with the precise fabrication of crowns, bridges, dentures, implants, and orthodontic appliances, labs are navigating a period of intense transformation. This flux is driven by the relentless advance of digital technologies, shifting market structures, and persistent operational pressures that demand new levels of efficiency and adaptability. While the US market size hovers around $7.2 billion and has seen modest compound annual growth of 1.9% over the past five years, this stability belies the significant underlying changes reshaping the competitive landscape.
Several powerful forces are converging to redefine the dental lab sector. The digital transformation, encompassing intraoral scanners (IOS), computer-aided design/computer-aided manufacturing (CAD/CAM), and 3D printing, is no longer a futuristic concept but an operational imperative. Artificial Intelligence (AI) is rapidly moving from diagnostic aid to a practical tool within the lab, automating design, quality control, and workflow processes. Simultaneously, market consolidation is accelerating, fueled by the growth of Dental Service Organizations (DSOs) and private equity (PE) investment, which alters client relationships and competitive dynamics. Compounding these shifts are significant operational headwinds expected to intensify in 2025, most notably chronic staffing shortages and escalating overhead costs.
This analysis provides an overview of these critical trends and challenges, synthesizing data and observations to offer strategic considerations for dental lab owners, PE backed Dental Lab Organization (DLO) and it’s executives, investors, technology providers, and other stakeholders. Understanding these dynamics is crucial for navigating the complexities of the modern dental lab environment and positioning for future success. The following sections will delve into the digital imperative, the rise of AI, the pursuit of operational excellence, evolving market dynamics including DLO management, and a focused look at technology solutions aiming to address these challenges.
2. The Digital Imperative: Transforming Lab Workflows from Necessity, Not Novelty
The integration of digital technologies is fundamentally altering dental laboratory operations. While the promise of enhanced efficiency, accuracy, and collaboration is compelling, the reality of adoption presents a more complex picture.
2.1 State of Digital Adoption - A Mixed Reality
The dental industry is witnessing a clear upward trend in the adoption of digital tools. Intraoral scanners (IOS) are becoming more common in dental practices, with US penetration reaching 57%, and CAD/CAM technology is now a primary manufacturing method in approximately 80% of US dental labs. 3D printing is also rapidly gaining traction, particularly for models, surgical guides, and dentures. This shift reflects a growing recognition that digitalization is key to improving workflows and outcomes.
However, this digital wave has not yet fully submerged the traditional landscape. A significant portion of dental clinics globally—estimated at around 85%—still rely on conventional impression techniques. This indicates that while labs may be investing heavily in digital capabilities, the full benefits are often unrealized due to bottlenecks at the clinical interface. The transition, though steady, has been slower than initially anticipated, partly due to the time required for the industry to adapt and fully recognize the potential of digitization.
This disparity highlights a persistent digital divide. The potential of a fully digital workflow, from chairside scan to lab fabrication, is often hampered by the uneven adoption rates and varying proficiency levels among dental practitioners. Labs equipped with advanced digital technology may still receive a large volume of physical impressions or suboptimal digital scans, creating friction and inefficiency. The challenges cited by dentists for slower adoption—high initial costs, steep learning curves, and integration complexities—directly impact the lab's ability to leverage its own digital investments. Consequently, labs that actively support their clients' digital transition through training and education gain a significant competitive advantage.
2.2 Quantifiable Benefits of Going Digital
Despite adoption challenges, the advantages of digital dentistry for labs are substantial and increasingly well-documented:
- Efficiency & Time Savings: Digital workflows demonstrably shorten turnaround times (TAT). Studies show digital pathways can significantly reduce laboratory processing time compared to conventional methods, particularly for single crowns and implants. Labside digital workflows can be comparable in time to conventional impression-taking for the dentist, but the downstream lab processes are accelerated. Electronically transmitting digital impressions eliminates shipping delays associated with physical models. This efficiency translates not only to faster case completion but also potentially reduced chair time for patients.
- Accuracy & Quality: Digital impressions and CAD/CAM manufacturing generally yield more accurate and better-fitting restorations. The precision of digital scans minimizes distortions common with traditional materials, leading to fewer errors and adjustments. This improved accuracy is a major factor in reducing remake rates; labs often report significantly lower remakes for digitally initiated cases, sometimes below 1%, compared to traditional methods.
- Enhanced Communication & Collaboration: Digital platforms transform the way labs and dentists interact. Sending digital scans and prescriptions via cloud platforms or dedicated portals allows for instant data transmission and eliminates the need for paper forms. Tools enabling real-time case tracking, in-app messaging, and 3D model visualization facilitate clearer communication, quicker feedback on designs, and a more collaborative approach to case planning.
- Improved Patient Experience: Digital impressions eliminate the discomfort associated with traditional putty materials, particularly for patients with gag reflexes or dental anxiety. Faster treatment times, including the potential for same-day restorations in some workflows, enhance patient satisfaction. Furthermore, the ability to show patients 3D visualizations of their dentition and proposed treatment outcomes increases engagement and understanding.
- Cost-Effectiveness (Long-Term): While the initial investment in digital technology can be substantial, the long-term economic benefits are compelling. Labs save on consumable impression materials and shipping costs. More significantly, the reduction in remakes and adjustments directly translates to saved labor, materials, and operational costs, ultimately improving profitability.
2.3 Overcoming Adoption Hurdles
Successfully navigating the digital transition requires addressing several key obstacles:
- High Initial Investment: The cost of acquiring IOS scanners, 3D printers, milling machines, and associated software remains a primary barrier, particularly for smaller labs and practices. Programs like ScanUp, which bundle scanners with lab services, attempt to mitigate this entry cost.
- Learning Curve & Training: Both clinicians and lab technicians require training to master new digital skills, from proficient intraoral scanning to CAD software operation and equipment maintenance. Effective vendor support and dedicated lab training programs are crucial for easing this transition.
- Integration & Compatibility: Ensuring new digital tools integrate smoothly with existing Practice Management Software (PMS), imaging systems, and partner lab systems is critical. Compatibility issues between different scanner outputs and lab software can create significant workflow friction. The push towards "open" systems, which allow data exchange between different manufacturers' equipment, is vital for flexibility.
- Workflow Disruption & Resistance to Change: Implementing new technology inevitably disrupts established routines. Overcoming staff inertia, fear of the unknown, or discomfort with technology requires strong leadership, clear communication, team buy-in, and demonstrating the benefits.
- Data Security & Privacy: The shift to digital necessitates robust measures to protect sensitive electronic patient health information, complying with regulations like HIPAA or PIPEDA.
Achieving the full promise of digital dentistry demands more than just acquiring technology; it necessitates ecosystem alignment. A successful transition hinges on coordinated efforts between the dental clinic, the laboratory, and technology providers. This involves ensuring interoperability between systems, investing in comprehensive training for both clinical and lab teams, and establishing clear, digitally enabled communication protocols. The lab's digital readiness is intrinsically linked to its clients' capabilities. Solutions like EviSmart, which aim to connect disparate systems and automate data flow regardless of hardware or software, represent attempts to bridge these ecosystem gaps and unlock the true potential of end-to-end digital workflows.
3. AI's Arrival: Automating for Accuracy, Efficiency, and Insight
Artificial Intelligence is rapidly transitioning from a buzzword to a practical, value-adding tool within the dental laboratory landscape. Moving beyond its initial applications in radiographic diagnostics, AI is now being deployed to automate and optimize various stages of the lab workflow, promising significant gains in efficiency, accuracy, and consistency.
3.1 Current AI Applications in the Lab
Several key areas are seeing impactful AI integration:
- Automated Design: AI algorithms are increasingly capable of generating initial designs for restorations like crowns, bridges, inlays, and onlays with minimal human intervention. Platforms like 3Shape Automate report high acceptance rates (e.g., 92%) for their AI-generated crown designs. Solutions like EviSmart CAD also incorporate AI-powered crown design capabilities. This shifts the technician's role from designing from scratch to primarily verifying and refining AI proposals, significantly speeding up the design phase for standard cases.
- Automated Quality Control (QC): AI tools are being developed to automatically review incoming digital impressions (scans) and prescriptions before they enter the production workflow. EviSmart QC, for example, uses AI to check for common errors like missing or unclear margins, misaligned bites, incomplete prescription details, and generally low-quality scans, flagging problematic cases based on criteria customized for each lab. This upstream validation aims to catch errors at the source, preventing costly downstream issues.
- Workflow Automation: AI is enhancing broader lab management systems by automating routine administrative and logistical tasks. This includes automated case entry into lab management software (LMS), intelligent case scheduling, automatic file format conversions, and automated communication triggers like status updates or approval reminders.
- Production Optimization: AI algorithms are being applied to optimize the "nesting" process for both 3D printing and milling. Smart nesting software, such as EviSmart Nest, aims to arrange multiple restoration designs within a resin vat or zirconia puck/disc to maximize material utilization, minimize waste, and reduce overall machine runtime.
3.2 The Value Proposition of AI
The integration of AI into lab workflows offers several compelling benefits:
- Efficiency Gains: Automation of design, QC, and administrative tasks significantly reduces manual labor time. This frees up highly skilled technicians to focus on complex, high-value work like intricate case planning, final finishing, and quality assurance, rather than repetitive processes. Some platforms claim substantial time savings, potentially reducing turnaround times.
- Improved Accuracy & Consistency: AI excels at pattern recognition and adhering to defined parameters, potentially reducing human error in tasks like design generation and QC checks. AI can analyze complex datasets and identify subtle anomalies or inconsistencies that might be missed by manual review, leading to more predictable and reliable outcomes. This directly contributes to lowering remake rates.
- Cost Reduction: Efficiency improvements translate to lower labor costs per unit. Enhanced accuracy and automated QC reduce the frequency of costly remakes, saving both materials and chair time. AI-driven nesting minimizes waste of expensive resins and zirconia, further controlling material costs.
- Enhanced Decision Support: Beyond automation, AI can provide valuable insights to aid decision-making. This includes simulating treatment outcomes, suggesting optimal materials based on case parameters, or predicting potential issues based on historical data analysis.
3.3 AI Adoption Landscape & Future Outlook
Investment in dental AI is accelerating, and adoption rates, while still nascent, are growing, particularly in areas like diagnostics and automated design. Numerous companies, from established players like 3Shape to newer entrants like Pearl, Overjet, and Evident, are actively developing and marketing AI-powered solutions for both clinics and labs.
However, challenges remain. Training effective AI models requires large, high-quality datasets, which can be scarce in specific dental applications. Ensuring AI models scale efficiently to handle increasing data volumes and complexity without excessive computational cost is another hurdle. Integrating AI tools seamlessly into existing, often fragmented, lab workflows requires careful planning. Furthermore, concerns about the transparency of AI algorithms ("black box" problem) and the need for robust validation and continued clinical oversight are critical considerations for responsible adoption.
Looking ahead, AI is expected to become more deeply embedded in dental workflows. Future developments may include more sophisticated predictive analytics for anticipating restoration longevity or potential complications, AI systems suggesting optimal design modifications or repair strategies, and potentially greater integration with robotic automation in the manufacturing process.
A key realization emerging from current AI applications is their power in shifting quality control upstream. The most significant bottleneck and cost driver for many labs is dealing with suboptimal inputs—poor impressions and incomplete prescriptions—which lead to downstream remakes. AI tools like EviSmart QC, which focus on automatically validating these inputs before production begins, offer a fundamental advantage. By catching errors early, they prevent the cascade of wasted materials, labor, and time associated with fixing problems later in the process, directly addressing the root cause identified by labs.
Furthermore, current AI implementations strongly suggest a collaborative future between technology and technicians. AI is primarily automating repetitive, standardized tasks (like initial crown design, basic QC checks, file sorting, nesting) and providing analytical support. It generates proposals that often require human verification and refinement, or flags issues that need expert human judgment. The need for skilled, experienced dental technicians remains critical, particularly for handling complex cases, performing final aesthetic adjustments, ensuring overall quality, and managing the nuances that AI cannot yet replicate. AI is augmenting the technician's capabilities, not replacing them entirely.
4. Operational Excellence: The Non-Negotiable Foundation for Profitability
In an environment of increasing competition, technological disruption, and cost pressures, achieving operational excellence is no longer optional for dental laboratories; it is fundamental to survival and profitability. This requires a rigorous focus on efficiency, quality, and data-driven decision-making.
4.1 The Power of KPIs and Benchmarking
Effective management starts with measurement. Tracking Key Performance Indicators (KPIs) provides objective insights into a lab's performance, highlighting areas of strength and weakness, and enabling informed strategic adjustments. As the adage goes, "That which is measured improves". Regularly monitoring metrics related to production, quality, turnaround time, and costs allows labs to identify problems, implement solutions, and track progress over time.
Benchmarking—comparing a lab's KPIs against industry averages or top performers—is equally crucial. This provides context for performance data, revealing whether a lab is leading, lagging, or meeting industry standards. For DLOs, benchmarking across different lab locations using standardized definitions and analytics tools (like Jarvis Analytics) is essential for identifying best practices and addressing performance variances.
Table 1: Key Dental Lab KPIs & Industry Benchmarks
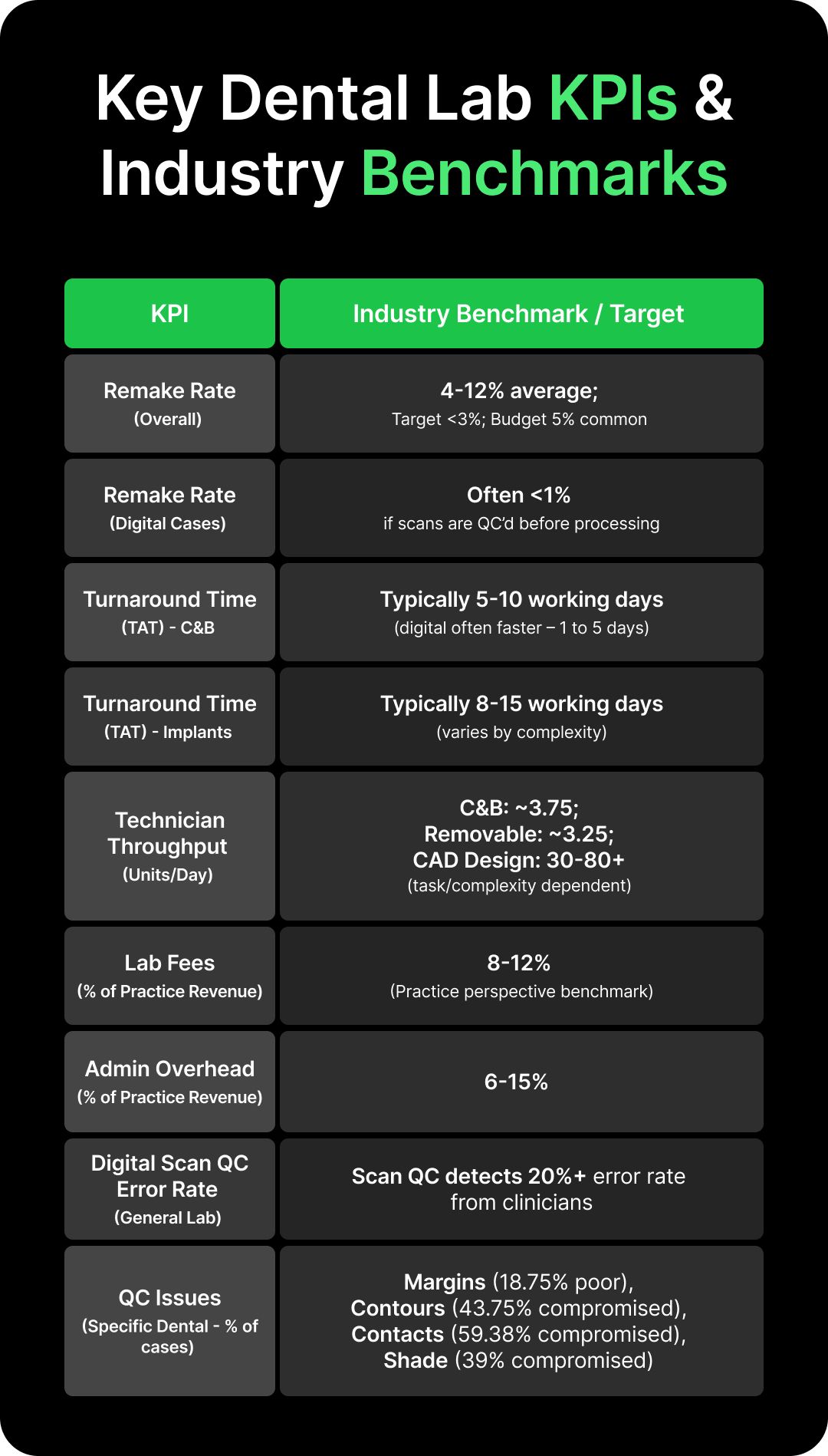
Note: Lab Fees and Admin Overhead are shown as % of Practice Revenue, as lab-specific overhead benchmarks are less commonly cited in the provided material. QC Error Rates vary widely depending on definition; medical lab data provides a general context, while dental-specific studies show higher rates for particular quality aspects.
This table provides a consolidated snapshot of critical performance targets. Labs can use these benchmarks to assess their performance relative to industry averages and identify areas requiring attention, such as high remake rates, slow turnaround times, low technician productivity, or disproportionate overhead costs. It grounds strategic discussions in quantifiable metrics, moving beyond anecdotal evidence.
4.2 The Remake Riddle - Causes, Costs, and Cures
Remakes represent one of the most significant drains on dental lab profitability and efficiency. Understanding their root causes, quantifying their financial impact, and implementing effective prevention strategies are critical.
Causes: The consensus among labs is that the majority of remakes originate outside the lab, with dentist error cited as the cause for approximately 82% of external remakes.
- Inadequate Impressions: This is overwhelmingly identified as the primary culprit. Specific issues include poor capture of preparation margins, voids, bubbles, or pulls in the material, material distortion (due to improper tray selection, premature removal, or patient movement), and contamination by blood or saliva. Impression rejection rates vary in studies, with some reporting alarmingly high rates of unacceptable impressions received by labs (e.g., 64.5%, 86-89% with errors), while others suggest lower clinical rejection rates.
- Communication/Prescription Errors: Incomplete, illegible, or ambiguous prescriptions are a frequent source of problems. Shockingly, some sources suggest 80% of dentists fail to complete all legally required information on Rx forms. Miscommunication regarding material choice, shade, or design specifications also leads to errors.
- Clinical/Design Issues: Problems originating from the clinical preparation or design instructions include inadequate tooth reduction (leaving insufficient space for restorative material), poorly defined margins, occlusal discrepancies, open or tight proximal contacts, and esthetic failures, particularly shade mismatch.
- Laboratory Errors: While less frequent according to lab surveys, errors within the lab do occur. These can involve material defects or improper handling, processing mistakes during fabrication, or failures in the lab's own quality control checks.
Cost: The financial impact of remakes is substantial, extending far beyond the cost of materials.
- Lost Dentist Chair Time: Remakes require additional appointments for adjustments, re-impressions, or re-seating, consuming valuable clinical time that could be used for revenue-generating procedures. Based on an estimated dental practice overhead of $375+ per hour, even a 20-30 minute adjustment or re-impression appointment represents a loss of $125-$187.50+ or more in opportunity cost for the dentist.
- Direct Lab Costs: The lab incurs the cost of wasted materials (e.g., zirconia pucks, resin, alloys), the labor hours spent on the failed case and the remake (estimated at $75+ per crown in one example), and additional shipping expenses.
- Profit Erosion: Remakes severely impact profitability. Depending on the lab's profit margin, it can take numerous successful cases (estimates range from 5 to 19 units) to financially recover from a single remake. A 5% remake rate can effectively wipe out the profit from a significant portion of a lab's work.
- Intangible Costs: Frequent remakes damage the lab's reputation, strain relationships with dental clients, and lead to patient frustration and dissatisfaction, potentially causing client attrition.
Cures: Reducing remakes requires a multi-pronged approach focused on improving inputs and processes:
- Improve Impression Quality: Emphasize dentist training on proper impression techniques and material selection. Encourage the adoption of digital impressions (IOS), which consistently show lower associated remake rates compared to traditional methods.
- Enhance Communication: Implement standardized digital prescription forms with mandatory fields to ensure completeness. Utilize high-quality photographs and digital visuals to convey shade, morphology, and case specifics accurately. Foster direct communication channels between dentists and technicians for case clarification and consultation. Leverage digital platforms for real-time messaging and case tracking.
- Leverage Technology: Adopt end-to-end digital workflows where possible. Implement AI-powered QC tools to automatically flag potentially problematic scans and prescriptions upon receipt, preventing errors from entering the production stream.
- Strengthen Partnerships & Feedback Loops: Cultivate strong, collaborative relationships with dental clients. Track remake rates per client and per product type to identify patterns. Provide constructive feedback to dentists on impression quality or prescription clarity, potentially using annotated photos. Clearly communicate and consistently apply the lab's remake policy (whether charging, splitting costs, or offering free remakes up to a certain threshold).
Table 2: Remake Causes & Estimated Financial Impact
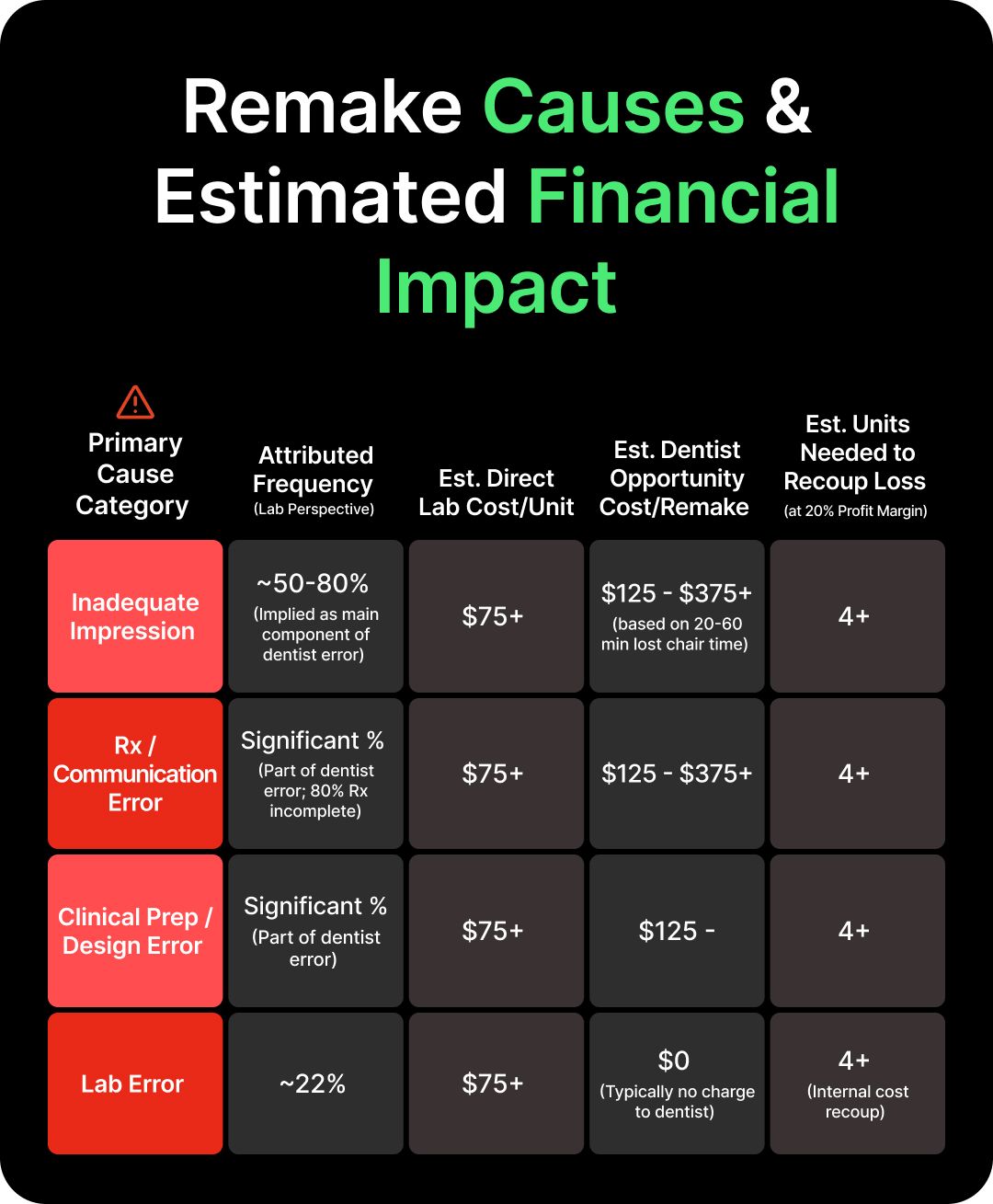
Note: Frequencies are estimates based on lab perspectives cited. Costs are illustrative based on provided examples and typical overhead/profit assumptions.
This table starkly illustrates the financial consequences of remakes originating from various sources. It underscores the critical need for labs to address the primary drivers—input quality and communication—to protect their bottom line and justify investments in preventative solutions like training, better communication tools, and AI-powered quality control.
4.3 Material & Workflow Optimization
Beyond remake reduction, optimizing material usage and streamlining internal workflows are essential for operational efficiency.
Material Management: Controlling the consumption of expensive materials like zirconia and 3D printing resins is crucial.
- Zirconia Nesting: Efficiently arranging restorations within a zirconia disc ("nesting") directly impacts material yield. While average labs might achieve 18-20 single units per standard disc, optimized nesting strategies, potentially aided by software or AI tools like EviSmart Nest, can push this to 24 units or more, significantly reducing per-unit material cost. Furthermore, exploring methods for recycling zirconia milling dust and block residuals presents an opportunity for cost savings and improved sustainability.
- 3D Printing Resin: Resin costs can constitute a large portion (up to 30-40%) of a lab's operating expenses for printed appliances. Implementing strategies like optimized support structures, efficient vat management, bulk purchasing, and potentially recycling initiatives can reduce material wastage by 10-20%. Faster printing technologies also improve overall throughput and efficiency.
- Inventory Control: Effective inventory management across all materials minimizes waste from expired or overstocked products and prevents production delays due to stockouts.
Workflow Automation: Leveraging software to automate non-productive, administrative tasks is key to maximizing technician time and reducing errors.
- Automated Intake: Manually downloading, converting, and sorting digital impression files from various scanner portals is a significant time sink. Tools like EviSmart Downloader automate this process, pulling files directly into the lab's workflow regardless of the scanner source, saving administrative time and reducing the risk of missed or duplicated files. While specific time benchmarks for manual intake are scarce, the potential savings are substantial for labs handling high digital volumes.
- Automated Case Entry & Scheduling: Software can automatically create new cases within the Lab Management System (LMS) based on incoming digital prescriptions and scans, assign tasks, and schedule production steps, eliminating manual data entry and reducing administrative burden.
- Integrated Communication & Tracking: Centralized digital platforms provide real-time case status visibility for both the lab and the dentist, facilitate case-specific messaging, manage design approvals, and automate notifications, drastically reducing the need for time-consuming phone calls and emails to track progress or resolve queries.
Table 3: Material & Workflow Efficiency Benchmarks

This table highlights tangible areas where labs can achieve significant operational improvements. Optimizing material yield through techniques like smart nesting and reducing waste via better inventory control directly impacts the bottom line. Similarly, automating time-consuming, non-value-added tasks like file intake and case entry frees up resources for core production activities.
Achieving peak performance requires a holistic view of the laboratory's operations. Implementing a state-of-the-art scanner or an AI design module will yield limited benefits if incoming cases are bottlenecked by manual intake processes or plagued by poor impression quality. True efficiency and profitability emerge when the entire workflow—from the initial dentist interaction and case acceptance, through material management, automated design and production, to final quality control and delivery—is optimized and integrated. This often necessitates adopting comprehensive, integrated software platforms capable of managing and automating processes end-to-end, coupled with standardized operating procedures. Solutions like EviSmart aim to provide this level of integration, connecting disparate systems to create a unified, efficient workflow.
5. Market Dynamics: Consolidation, Competition, and the 2025 Pressure Cooker
The dental laboratory industry operates within a rapidly evolving market characterized by significant consolidation, intensifying competition, and mounting operational pressures expected to continue through 2025.
5.1 The Consolidation Wave - DSOs, PE, and the Lab Landscape
A major force reshaping the dental ecosystem is the rise of Dental Service Organizations (DSOs) and the increasing involvement of Private Equity (PE) firms. Dentist affiliation with DSOs has grown substantially, reaching estimates of 13% to 23% nationally, with projections suggesting this could exceed 30-40% by 2030. This trend is driven by factors like dentists seeking relief from administrative burdens, access to capital and technology, and exit strategies for retiring practitioners.
This consolidation has profound implications for dental labs. DSOs, leveraging their scale, often seek laboratory partners capable of handling large volumes, ensuring consistent quality across multiple locations, and providing competitive pricing, frequently demanding volume discounts. This dynamic favors larger, technologically advanced labs or DLOs (Dental Lab Organizations) that can meet these demands. Concurrently, the number of small, sole-proprietor labs has dramatically declined, squeezed by the need for capital investment in technology they often cannot afford and increased competition. The dental lab market itself is also consolidating, with larger labs acquiring smaller ones and PE firms backing platform acquisitions to build scale.
This wave of consolidation appears to be driving market polarization. The industry seems to be bifurcating into two main segments: large, highly efficient, technology-driven labs and DLOs equipped to serve the needs of large DSO clients and high-volume practices, and smaller, perhaps niche or boutique labs that survive by focusing on specialized, high-value restorations, strong local dentist relationships, or markets less dominated by DSOs. Mid-sized labs lacking clear differentiation, significant technological investment, or strong niche positioning may find themselves increasingly squeezed by price pressures from below and the scale advantages of larger competitors above. This two-polar model, predicted by some industry observers, suggests that strategic positioning—either towards scale and efficiency or towards specialized value—is becoming critical.
5.2 Headwinds for 2025 - The Top Industry Challenges
Looking ahead to 2025, dental labs face a confluence of significant challenges:
- Staffing Shortages: This remains a paramount concern across the dental industry, impacting both clinics and labs. Labs specifically struggle to recruit and retain skilled dental technicians, a problem exacerbated by the decline of formal training programs and perceived unattractiveness of the trade. This shortage increases workload on existing staff, contributes to burnout and turnover, drives up wages, and hinders a lab's ability to scale production or adopt new technologies that require trained personnel. While increased graduation numbers from dental hygiene programs might offer some relief on the clinical side, the technician shortage appears more persistent.
- Rising Costs & Economic Pressure: Labs are grappling with increasing overhead costs for materials, utilities, and labor. This is compounded by broader inflationary pressures and potential price pressure from large clients like DSOs. Dentists themselves face similar cost increases alongside potentially stagnant or declining insurance reimbursements, which can indirectly affect lab case volume or pressure lab fees. Potential import tariffs on dental equipment and materials could further exacerbate cost challenges.
- Technology Investment Pressure: The need to invest in digital workflows, automation, and AI to remain competitive, improve efficiency, and meet client expectations is undeniable. However, the high cost of this technology creates a significant financial hurdle, especially for smaller labs already facing tight margins and economic uncertainty. Deciding where and when to invest limited capital becomes a critical strategic challenge.
- Regulatory & Compliance Burden: Operating a dental lab involves navigating an increasingly complex regulatory environment. This includes ensuring compliance with FDA regulations for medical device manufacturing (including quality systems/GMPs for labs milling or printing restorations), adhering to data privacy laws like HIPAA (and PIPEDA for labs with Canadian operations or clients) when handling patient information digitally, and potentially meeting state-specific licensure or registration requirements. The costs and administrative overhead associated with maintaining compliance add another layer of operational pressure.
The persistent staffing crisis serves as a powerful catalyst driving the adoption of automation and AI technologies within dental labs. Faced with the ongoing difficulty of finding and keeping skilled technicians, labs are increasingly motivated to invest in technologies that can amplify the productivity of their existing workforce. Automation tools that handle repetitive, time-consuming tasks like file intake, basic design, QC checks, and nesting allow skilled technicians to focus their expertise on more complex, value-added activities. AI can also help ensure consistency and quality, potentially reducing the training burden or reliance on highly experienced personnel for certain tasks. Thus, the labor shortage, while a significant challenge, is concurrently accelerating the technological evolution of the industry by making automation a strategic necessity, not just an option.
5.3 Managing the Multi-Site DLO - Challenges of Scale
Dental Lab Organizations (DLOs) managing networks of multiple labs face unique operational complexities beyond those of single-location entities. Successfully scaling requires addressing challenges related to:
- Standardization: Achieving consistency in processes (e.g., case intake, production workflows), quality standards, material usage, equipment calibration, and even branding across geographically dispersed labs is paramount for delivering predictable results and maintaining the DLO's reputation. This often necessitates centralized development and enforcement of Standard Operating Procedures (SOPs) and potentially shared technology platforms.
- Communication & Collaboration: Effective communication is vital to coordinate activities, share best practices, and resolve issues across different lab sites, potentially spanning different time zones or cultures. Siloed information hinders efficiency and consistency. Robust digital communication channels and regular inter-lab meetings are essential.
- Data Management & Integration: Integrating data from potentially disparate systems (LMS, CAD/CAM, financial software) across multiple labs is a major challenge. Achieving centralized reporting and analytics is crucial for monitoring performance, comparing labs, identifying trends, and making informed management decisions. This drives the need for management platforms with multi-site capabilities, allowing data aggregation and standardized reporting from a single dashboard.
- Quality Control & Performance Variance: Ensuring consistent product quality and managing inevitable performance variations between different labs within the DLO network is critical. This requires clear, measurable quality benchmarks, potentially centralized QC processes or audits, and tools to track and compare key metrics like remake rates and TAT across locations.
- Training & Competency: Maintaining a consistently skilled workforce across all sites requires standardized training programs for new hires and ongoing professional development to ensure proficiency with shared procedures and technologies.
The inherent complexities of managing standardization, communication, data integration, and quality control across multiple sites make centralized technology platforms increasingly essential for DLOs. Integrated, potentially cloud-based systems that offer multi-site management capabilities—allowing standardized data collection, centralized reporting, shared workflows, and unified communication—become critical infrastructure for achieving operational efficiency, maintaining quality consistency, and enabling scalable growth. Platforms like EviSmart, with their focus on connecting systems and providing centralized dashboards and reporting, aim to address these specific DLO needs.
6. Focus on EviSmart: A Case Study in Lab Workflow Automation
Amidst the technological shifts and operational challenges facing the dental lab industry, platforms like EviSmart by Evident Digital have emerged, aiming to provide comprehensive workflow automation solutions. Understanding its features and positioning offers insight into the direction of lab technology.
6.1 Overview
Evident Digital, founded in 2007 and headquartered in Vancouver, Canada, positions itself as a company focused on simplifying dental technology by connecting fragmented workflows. Its flagship offering, EviSmart, is described as an AI-powered dental workflow automation platform designed to connect labs, clinics, and potentially manufacturers. The core value proposition revolves around improving efficiency, reducing errors (like remakes), enhancing collaboration, and enabling labs and clinics to scale their operations. A key aspect emphasized is its ability to integrate with existing hardware and software systems, aiming to avoid costly rip-and-replace scenarios for users.
6.2 Key Modules & Features
The EviSmart platform appears to be modular, addressing different stages of the lab workflow:
- EviSmart Downloader: Automates the retrieval and import of digital impression files from various intraoral scanners and external portals directly into the lab's system. Features include customizable download locations and file naming conventions. This module aims to eliminate manual downloading and sorting, saving administrative time and reducing the risk of lost or duplicated scan files.
- EviSmart QC: Utilizes AI to automatically review incoming prescriptions and scans based on customized criteria set by the lab. It flags potential issues like poor scan quality (e.g., missing margins, misaligned bites) and incomplete or unclear prescription information before cases enter production. The goal is to improve accuracy and reduce rework by catching errors early.
- EviSmart CaseEntry: Automates the creation of new cases within the lab's existing management software, potentially integrating with scheduling and ensuring case updates are synchronized across the platform.
- EviSmart LMS (Lab Management System features): Includes capabilities for automated case scheduling, integration with communication tools (EviSmart Comm), automated payment processing, and the generation of customized automated reports.
- EviSmart CAD: Facilitates integration with outsource CAD design services, enables touchless case triage (potentially routing cases automatically based on complexity or type), incorporates AI-powered crown design, and allows for customizable QC checkpoints within the design phase.
- EviSmart Comm: Provides a platform for case-specific messaging and design approvals between the lab and clinic. It integrates with the LMS and other systems and is designed to be HIPAA and GDPR compliant. A mobile app component allows dentists to review designs in 3D and provide feedback via annotations or messages.
- EviSmart Nest: Automates the nesting process for both 3D printing and milling, aiming to optimize material usage (resins, pucks, discs) and reduce production time. It also includes features for connecting with outsource manufacturing partners and general production optimization tools.
- Multi-Site Capabilities: While not explicitly detailed as a separate module, the platform's emphasis on connecting systems, centralized data (implied by reporting features), automated workflows, and dashboard views suggests capabilities suitable for DLOs needing to manage and monitor performance across multiple lab locations.
6.3 Implementation & Support
Evident outlines a three-step implementation process for EviSmart:
- Mapping the client's existing workflow,
- Identifying bottlenecks and creating a personalized improvement plan,
- Connecting EviSmart to the client's existing software and hardware. The company claims quick onboarding is possible. Support appears to involve access to industry experts, potentially including CAD designers, and user training is implied as part of successful adoption. Contact information for support (phone, email) with specified hours (Mon-Fri, 6 am-5 pm PST) is provided. Compliance with data privacy regulations like HIPAA and PIPEDA is stated for relevant modules like EviSmart Comm.
6.4 Quantified Benefits & Testimonials
Evident promotes significant benefits from using EviSmart, although some specific quantitative claims originate from potentially inaccessible sources and should be viewed with that context. General claims include working up to 10x faster with fewer errors. Testimonials from lab executives and dentists highlight key perceived advantages: improved efficiency and speed ("workflow has become speedy and efficient"), increased accuracy ("100% accuracy" in catching portal cases), reduced stress levels, improved profitability (Frontier Group citing a 30% improvement), better communication and collaboration, and faster turnaround times enabling better patient care. These testimonials suggest the platform effectively addresses common lab pain points related to manual processes, communication gaps, and production bottlenecks.
7. Conclusion: Strategic Imperatives for Dental Labs in 2025
The dental laboratory industry is navigating a period of profound change, characterized by the rapid acceleration of digital technologies and AI, intensifying market consolidation, and significant operational pressures, particularly around staffing and costs. The analysis reveals several critical imperatives for labs aiming to thrive in 2025 and beyond.
The digital transformation is no longer optional but a prerequisite for competitiveness. While adoption varies, the benefits of digital workflows—enhanced efficiency, improved accuracy, reduced remakes, better communication, and superior patient experiences—are clear. However, realizing these benefits requires more than just purchasing equipment; it demands an ecosystem approach involving close collaboration between labs, dentists, and technology providers to ensure interoperability and effective utilization. The persistent digital divide between lab capabilities and clinical adoption highlights the need for labs to actively support their clients' digital journey.
AI is emerging as a powerful tool to augment lab capabilities, particularly in automating routine tasks and enhancing quality control. Its most immediate impact lies in shifting QC upstream—using AI to validate incoming scans and prescriptions, thereby addressing the primary source of costly remakes. This complements, rather than replaces, the crucial skills of experienced technicians, who can then focus on more complex and value-added aspects of restoration fabrication.
Operational excellence, underpinned by rigorous KPI tracking and benchmarking, is non-negotiable. Labs must relentlessly focus on efficiency, particularly in managing the high cost of remakes by improving input quality and internal QC processes. Optimizing material usage through techniques like smart nesting and effective inventory management is also vital for profitability. Integrated workflow automation platforms offer significant potential to streamline operations from end to end, reducing administrative burden and maximizing productive time.
Market consolidation, driven by DSOs and PE, is polarizing the industry. Large, efficient, tech-enabled labs are positioned to serve high-volume clients, while smaller labs must find defensible niches or risk being squeezed out. Simultaneously, the persistent staffing crisis creates a strong incentive for labs of all sizes to invest in automation and AI to maintain or increase output despite labor constraints. For DLOs, managing multiple sites effectively necessitates centralized platforms, standardized procedures, and robust systems for ensuring consistency in quality and performance across their network.
Based on these dynamics, several strategic considerations emerge for dental labs:
- Invest Wisely in Technology: Prioritize integrated, interoperable digital and AI solutions that address key bottlenecks—particularly incoming QC, communication, and workflow automation. Evaluate ROI carefully, considering long-term efficiency gains and remake reduction.
- Master Operational Metrics: Implement comprehensive KPI tracking (Remakes, TAT, Throughput, Costs). Benchmark rigorously against industry standards and internal goals. Make remake reduction a primary focus through proactive quality management of inputs.
- Elevate Dentist Partnerships: Move beyond a transactional relationship. Actively communicate, provide digital support and education, and collaboratively define expectations and protocols. Position the lab as a strategic partner in delivering quality patient care.
- Embrace Automation & AI Strategically: Target AI and automation for high-volume, repetitive, or error-prone tasks first (e.g., incoming QC, basic design, nesting, file management). Invest in upskilling technicians to leverage these tools effectively.
- Address Staffing Proactively: While recruitment remains challenging, focus on retaining existing talent through training, supportive work environments, and competitive compensation. Leverage technology to maximize the productivity and efficiency of the current team.
- (For DLOs): Invest in centralized management platforms that enable standardization, unified reporting, seamless communication, and consistent quality control across all locations.
The dental lab industry faces undeniable challenges in 2025, but also significant opportunities. Success will belong to those labs that strategically embrace technological innovation, relentlessly pursue operational efficiency, cultivate strong partnerships, and adapt nimbly to the evolving market landscape.
As the industry continues to evolve, the dental labs that embrace integrated digital workflows, automation, and AI will be the ones that thrive — not just survive. At Evident, we built EviSmart to help labs do exactly that:
EviSmart: Intelligently Connecting Dental Workflows. Simple. Powerful. Scalable.
---
About the Author:
Paolo Kalaw is the Chairman and CEO of Nimbyx, a venture firm advancing AI-driven healthcare innovation across North America and Southeast Asia. He also leads Evident, the global benchmark in AI-powered dental automation. With a track record of scaling technology companies and a focus on intelligent systems that drive real-world outcomes, Paolo is at the forefront of applying AI to transform industries with precision and purpose.
Connect with Paolo on LinkedIn to explore the future of AI, automation, and healthcare innovation.
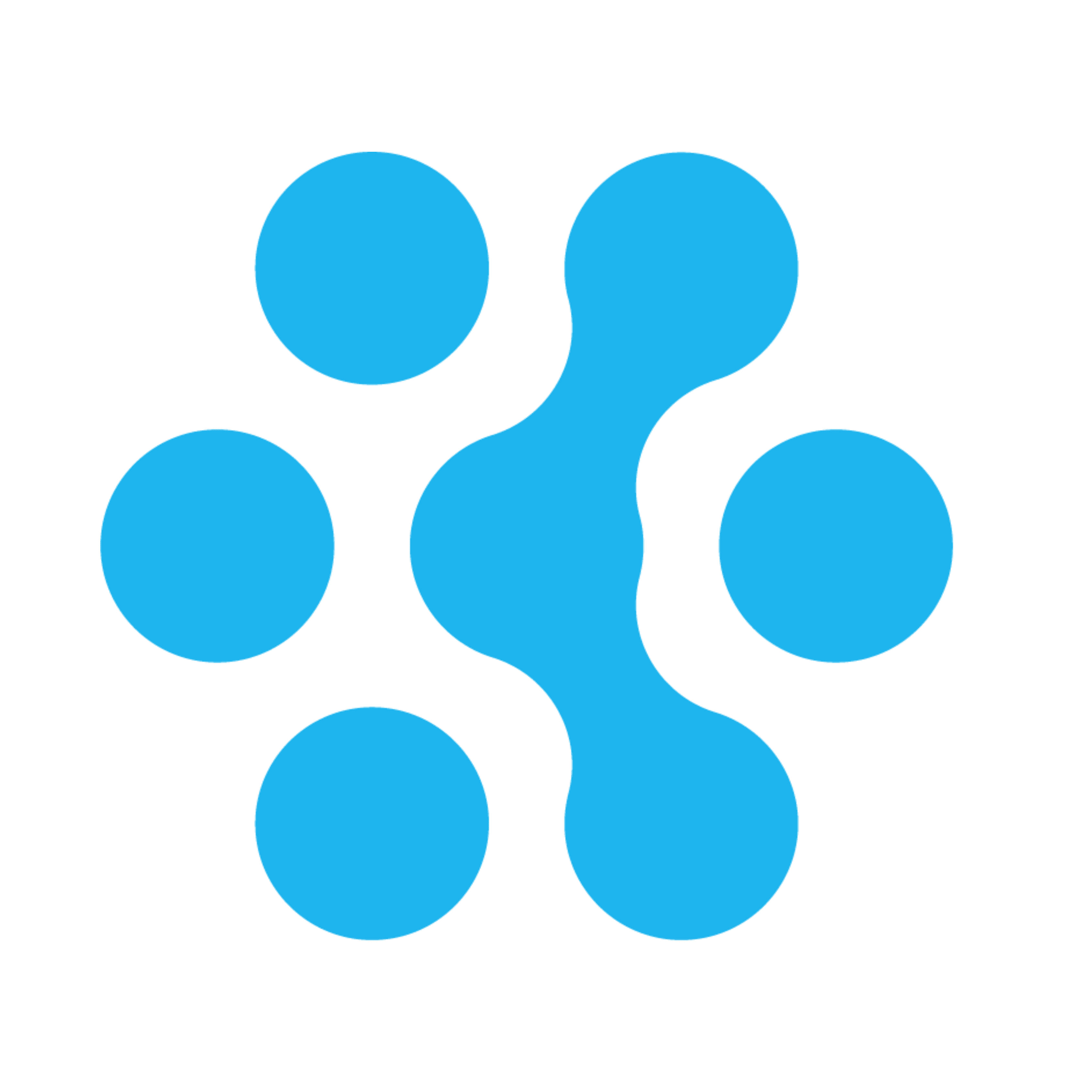